
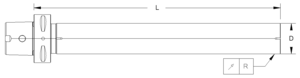
Coromant Capto C6 coupling is comparable to HSK 100, but a C8 coupling (circa 55,000 N) or a C10 coupling (around 75,000 N) clearly provide a far higher clamping force. HSK 63 couplings fall somewhere in the middle of these clamping forces (according to the HSK handbook 1999), while HSK 100 provides a maximum clamping force of 43,570 N.
#Spindle capto plus#
And the results were striking: none of the competing toolholding systems could achieve even close to the same results as the Coromant Capto coupling.Īmong other things, the study showed that the larger wall thickness of Coromant Capto in comparison to HSK allows for higher clamping forces, and these higher clamping forces translate into increased bending stiffness.Īccording to BIG Daishowa, the BIG Plus CAT 40 coupling has a maximum clamping force of around 10,000 N, while BIG Plus CAT 50 increases this figure to 25,000 N. A test performed by the university’s machine tool laboratory (WZL) compared the bending stiffness and torque resistance of Coromant Capto to that of other sizes of standard couplings. RWTH Aachen University in Germany carried out a study of Coromant Capto and comparable toolholding systems. Other influential coupling characteristics include cross-sectional area, where a reduction of the tool diameter relative to the flange contact diameter will reduce tool stiffness. Spindle nose/toolholder flange face contact increases the ‘platform base’, thus reducing the leverage of the cutting force, with the greater the clamping force to restrain a coupling, the greater is the cutting force required to ‘topple’ it. Two of the main requirements/limitations of a coupling are: bending stiffness – challenged by long tools or through high cutting forces and torque transmission – force times rotating cutter radius. The improved radial precision and torque transmission serves not just the demands for machining centres, but also turning centres, multi-tasking turn-mill machines and vertical lathes, for both rotating and static tooling. The third coupling, developed during the same period, is Sandvik Coromant’s Coromant Capto ( which brings together the benefits of both HSK and Big Plus, but removes the need for drive keys by instead employing a tapered polygon shaft. This extra clamping force makes the radial stiffness of HSK toolholders up to five times greater than the value for 7/24 taper systems, so more resistant to bending.īIG Plus, developed in Japan by BIG Daishowa and a 7/24 taper variant, boasts tighter manufacturing tolerances that allow spindle nose/tooholder flange and spindle bore/toolholder taper contact, but it still employs pull studs for clamping. Depending upon the variant, they have drive keys, except for some high spindle speed styles.Īssuming that equivalent force is applied to the drawbar, twice as much clamping force is exerted on the flange of an HSK shank compared to a steep taper shank. Intended for higher speed machining centres, it features toolholder flange/spindle nose contact and hollow taper segment clamping, thus removing the need for pull studs. For instance, in 1992, HSK was developed in Germany by the DIN committee. As a result, more developments came to market. The drawback with 7/24 steep taper interfaces is a lack of bending stiffness and rpm capability, due primarily to low clamping force (effected via a pull stud) and insufficient face contact between the toolholder and spindle nose face. Gripper grooves and pull studs were added for tool change purposes in the 1960s, with three main regional variations: MAS-BT (Asia) ISO/DIN (Europe) and CAT-V (America).
#Spindle capto iso#
Thereafter, the 7/24 steep taper (also called ISO taper) was introduced in 1927. The first well known interface was the Morse taper, developed for drilling as far back as 1868. Spindle/toolholder interfaces have evolved considerably over the years. The most appropriate choice of spindle interface comes down to the required bending stiffness and clamping force. The latter is, in fact, standardised as ISO/DIS 26623, meaning that other toolholder makers can supply it – WNT (01) and Sumitomo Electric Hardmetal (01844 342081), for example.
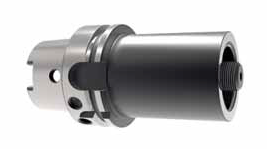
There are many machine spindle/toolholder interfaces, including HSK, Big Plus and Coromant Capto.
